How Direct Air Capture works at Carbon Engineering
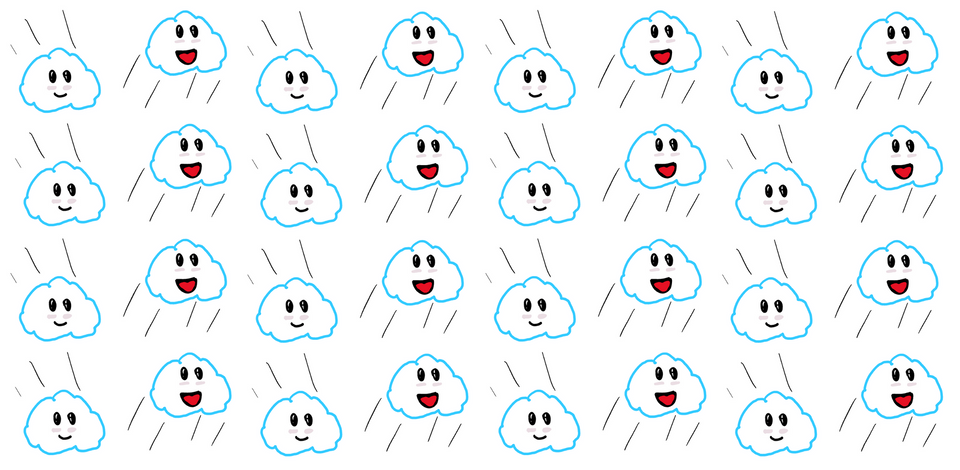
Carbon Engineering is one of the most prominent Direct Air Capture companies with their upcoming 1MtCO2/year capacity plant that is ready to be released in 2024.
Back in 2018 they released a detailed paper where they explained their process so that they could defend their claims of bringing the cost of capture to 94-232$/ton CO2. You can read the paper yourself to get a lot of very interesting insights but what I’ll do in this post is that I’ll try to explain the process to someone like me: clueless about chemistry and industrial processes but eager to understand how this CO2 capture magic works.
The loops
They have a great diagram that abstracts the entire process in two main loops:
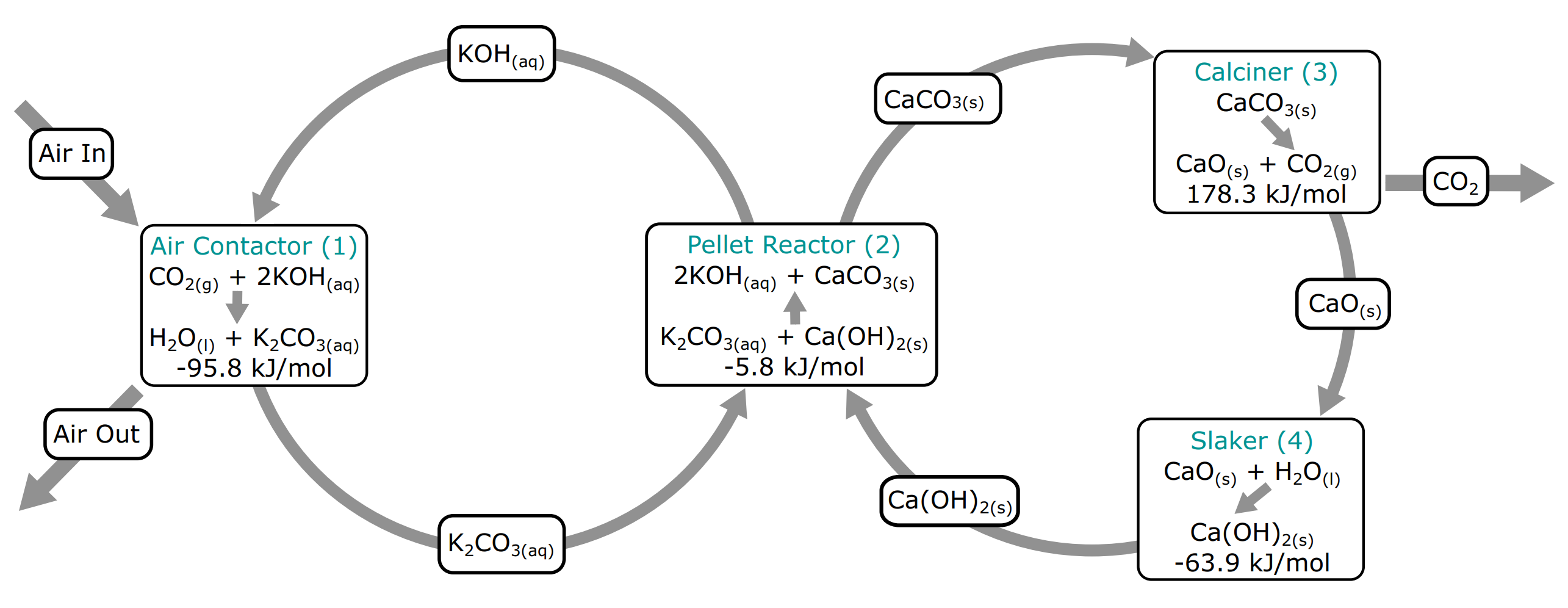
If it seems overwhelming, the main things to keep in mind are that these two loops have two purposes:
- The left one’s purpose is to capture the CO2 from the air
- The right one’s purpose is to deliver the CO2 from its captured state to outside of the plant
The reasons why we have two loops, instead of one where the above two steps happen are:
- Economy of scale by using existing processes and components (“calcination” as it’s been used in in the cement industry for decades)
- Reusability of chemical compounds to bring costs down
Don’t worry, it will all make sense soon.
First, let’s get started with the reactions.
1. CO2 capture with KOH
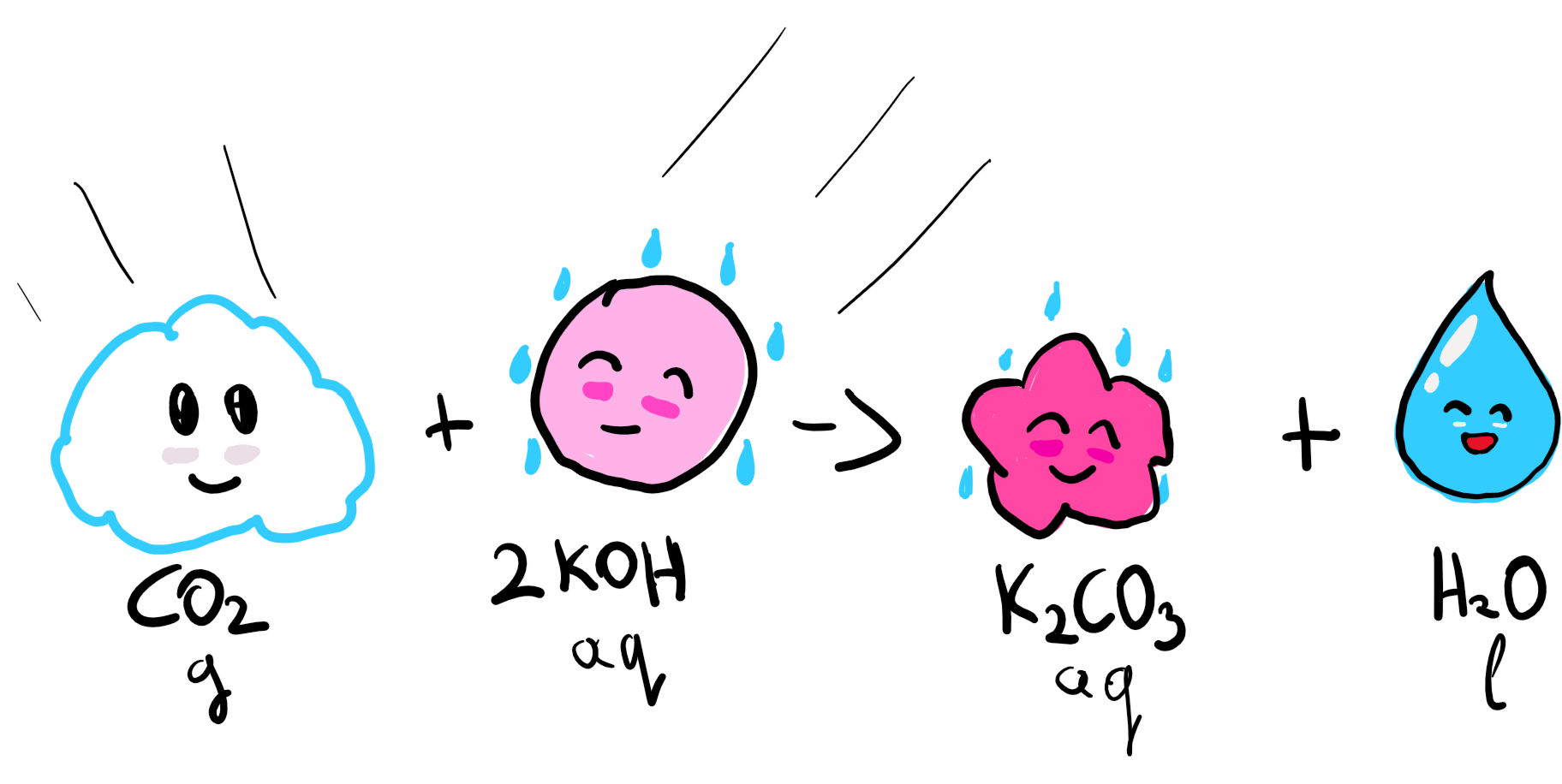
In the Air Contactor, our CO2 reacts with KOH, or Potassium Hydroxide, which is a very reactive solvent (you might remember its cousin, NaOH which was used in the famous hand burn scene in Fight Club so, yeah, not the friendliest of compounds) and produces water and K2CO3, or Potassium Carbonate, which is a compound used in soaps.
The reason why we need such a strong solvent is because, remember, the concentration of CO2 in the air is low at around 400ppm.
2. Production of CaCO3
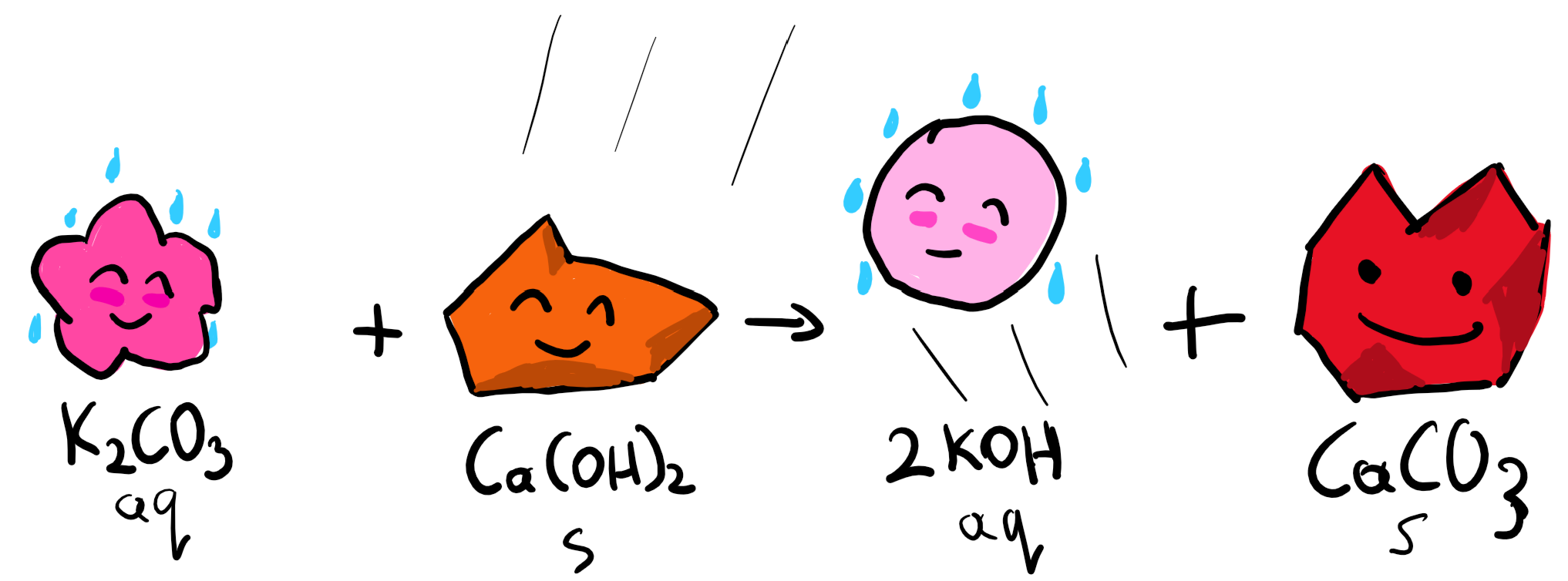
Of course, Carbon Engineering is not in the soap making business (though others are), so the K2CO3 is reacting with Ca(OH)2 pellets in the pellet reactor in order to:
- Regenerate KOH which goes back to the Air Contactor in order to help capture more CO2 and not lose money on the way.
- Generate CaCO3 pellets to then feed into the calcination process.
3. Burning of CaCO3 and release of CO2

This process is a very common one in the cement industry where CaCO3 together with some other materials are entered in a very high-temperature rotating kiln to produce cement. This means that there are already many components in place, specifically the Calciner which is important when you’re building a plant (and you plan to scale to more plants) of the scale of 1MtCO2/year.
Here, our CO2 is released from our chain of reactions and pressurized to turn into liquid and transferred wherever it needs to go.
4. Regeneration of Ca(OH)2
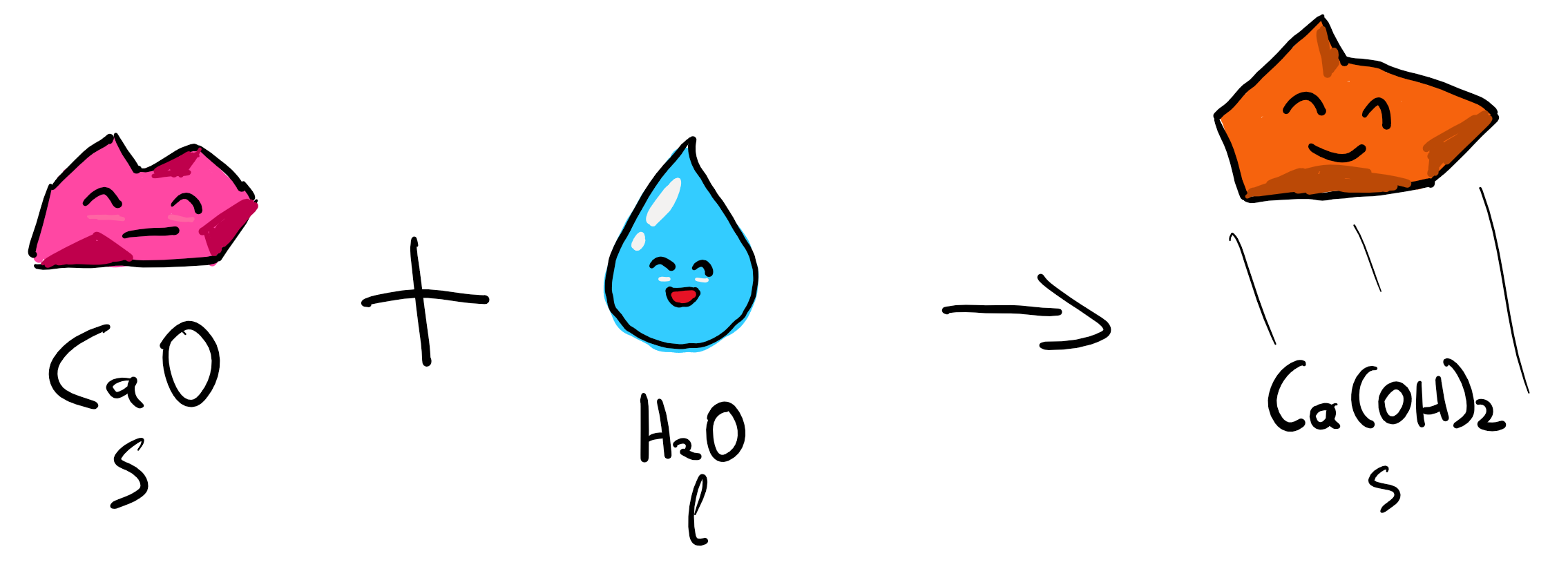
We are not done yet, as the compound that is used in order to make the CaCO3 two reactions above can be regenerated by steaming the CaO, or Calcium Oxide, thus helping us save more money. This is happening in what is called a “slaker” and is our last reaction.
The components
Of course, there is more involved than just the chemistry in the building of such a plant and this includes the machines. The heavy, industrial grade machines that are arranged in complex layouts like this:
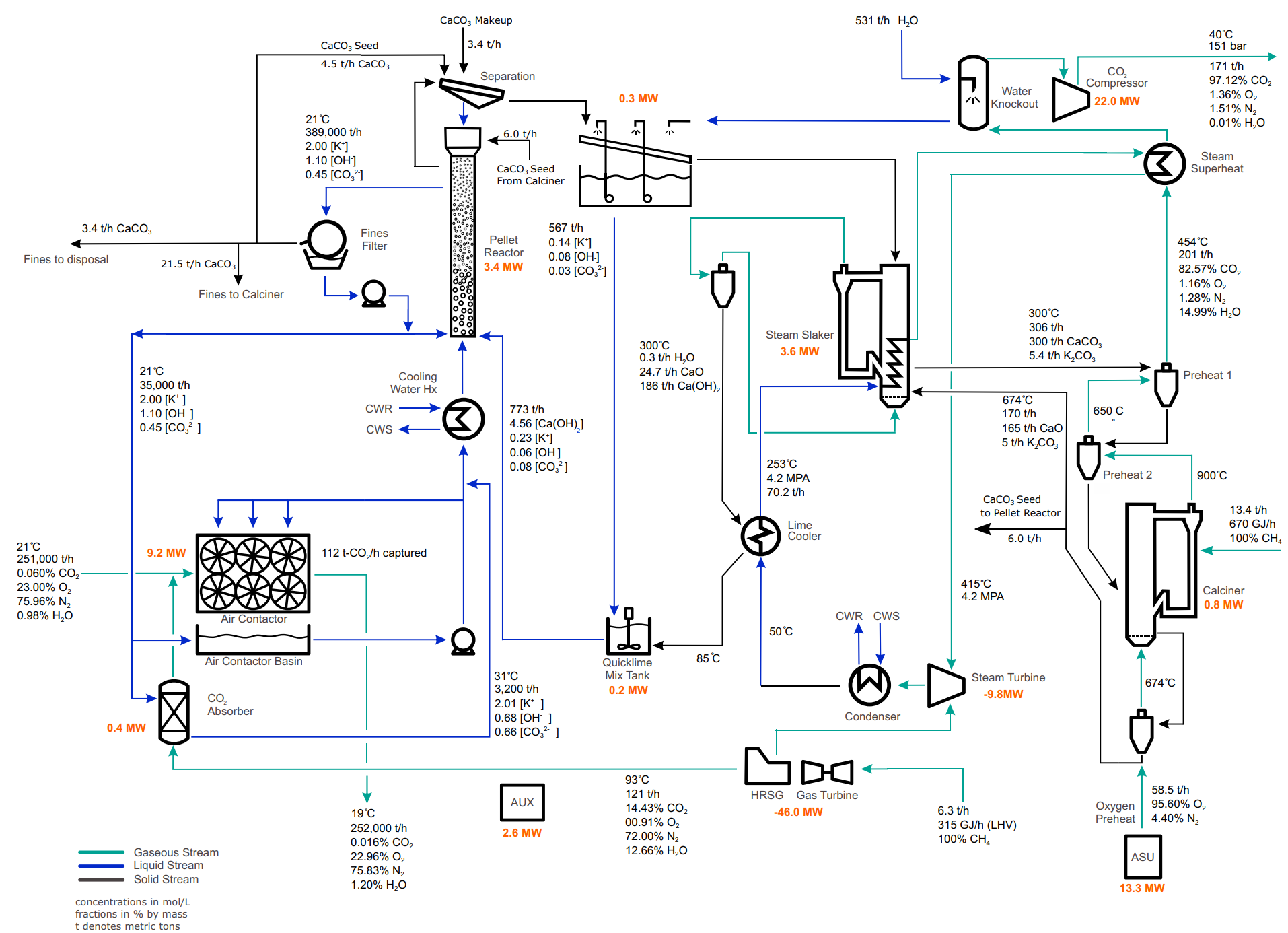
At the cost of omitting a lot of the beautiful work the process engineers did, I'm going to try to explain how their machines work across the whole process, specifically the four main ones:
Air Contactor
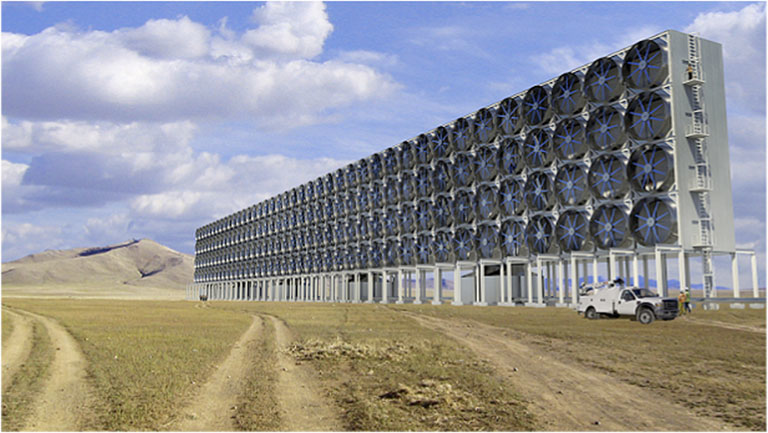
This photogenic component is probably the most common picture you bring up in your mind when someone tells you about Direct Air Capture plants.
CE have gone through a lot of research to come up with the optimal dimensions and have also published a paper around this.
The reason why it's shaped like that is because:
- At CO2 concentrations of 0,04% in the atmosphere you need to suck in a lot of air in order to tally to that 1 million Carbon Dioxide score at the end of the year. That's why it needs to be wide, 20m by 200m in particular.
- After the fans, the air flows through very narrow honeycomb-shaped holes of a very compact plastic material (like these ones), which is wetted by the capture liquid (KOH). Because the diameter is so small, there is a significant air pressure drop which basically means that the air slows down, which then means more energy to push the air through. That's why the depth of the Contactor can't be big but just enough to allow for enough time for the solvent to react with the air and the velocity to drop just a bit. They found this number to be about 10 meters.
Pellet Reactor
This is a machine where CaCO3 is created in the form of small (0,1 - 0,9mm) solid white pellets. This is a custom component of theirs, adapted from wastewater treatment, where traditionally you would have the formation of "lime mud" instead of pellets. Because the latter are drier than the former you can burn them at a relatively lower temperature in order to extract CO2, in the next step.
Calciner
This is where our Carbon Dioxide is "released" from the plant to be delivered to its next target (sequestration or usage) by burning the aforementioned CaCO3 pellets and also producing CaO. The needed temperatures are at about 900C so you can't just turn up your home's oven but you'll need to burn pure oxygen to reach these temperatures which then dictates the need of a process to separate it from the air (which, as a reminder, contains more N than O).
Steam Slaker
This is the last part of the process where in high temperatures (300C) the CaO that is produced above reacts with water (steam, more precisely) to create Ca(OH)2.
As a reminder, Ca(OH)2 is what reacts with K2CO3 which:
- Kicks off the beginning of the right loop process by generating CaCO3
- Regenerates our Carbon Dioxide capture solvent, KOH
Regenerating our compounds and solvents are important for reaching economies of scale, even if the processes become very tangled.
Total Costs
At the end of their paper, CE give an estimate of each plant which, you won't be excited to hear, go up to about 1B dollars. Every subsequent plant will be "cheaper" at around 700 millions.
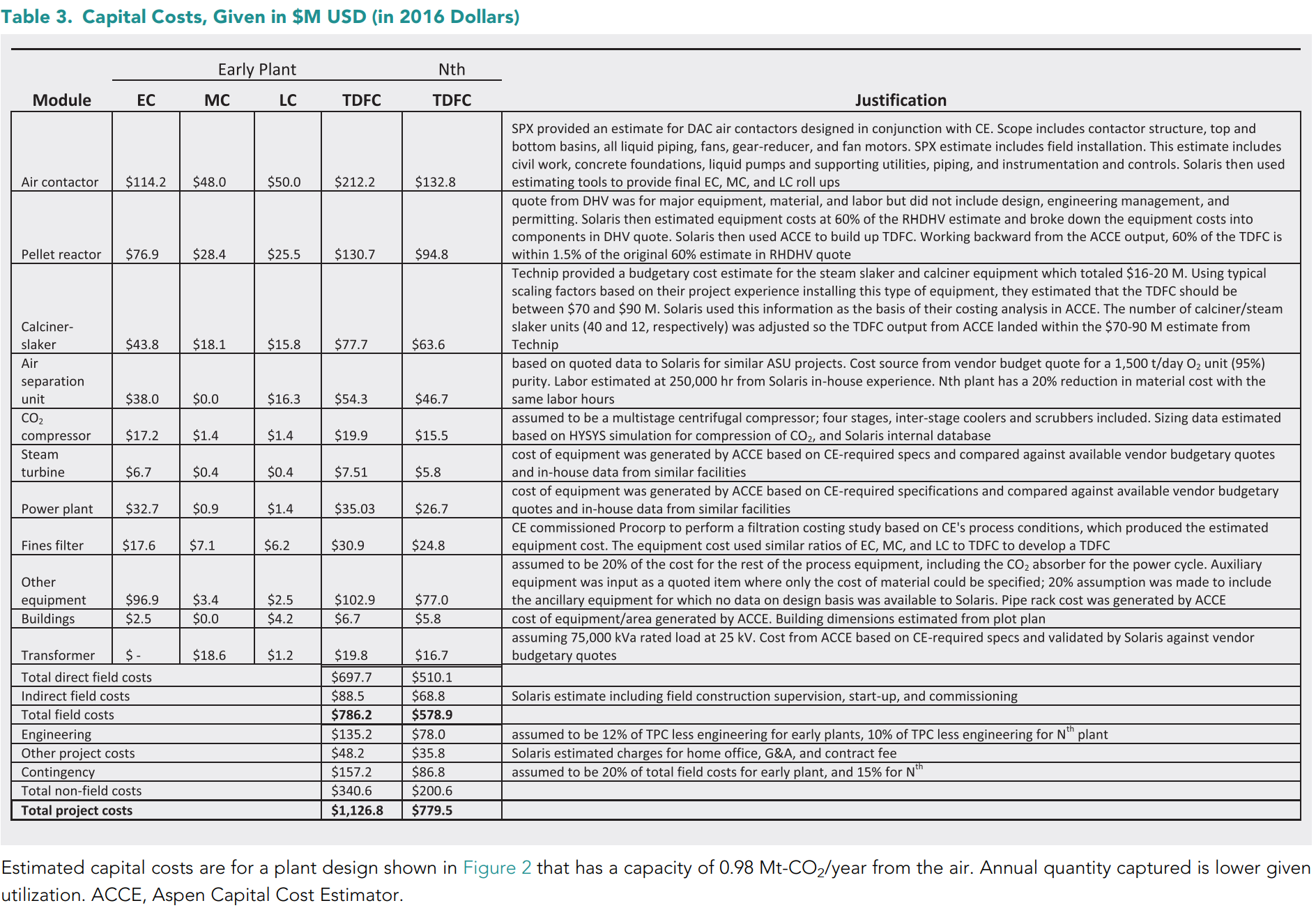
These numbers might seem outrageous, especially since they amount to just 0,1% capture of 1Gt CO2 (and remember, we emit about 50Gt per year) - with just a small calculation we see that we would need to spend about 1 trillion dollars just to capture 1GtCO2/year (80 trillions are the yearly worldwide GDP).
But, remember that as technologies scale, their costs go down, so it's positive that some companies are picking up the tab so that the rest of us can take advantage of successful innovations, tried configurations and established supply chains.
We also have other ways that we can capture CO2, such as:
- Physical capture
- Cryogenic capture
which I'll explain in future posts.
Sign up to receive them in your inbox and Merry Christmas to everyone! 🎅